Opening Quality: Aluminum Casting Techniques & Tips for Superior Outcomes
Opening Quality: Aluminum Casting Techniques & Tips for Superior Outcomes
Blog Article
Introducing the Various Sorts Of Light Weight Aluminum Spreading Processes for Accuracy Results
From die casting to sand casting, investment spreading, irreversible mold casting, and centrifugal casting, each approach brings its very own collection of complexities and benefits to the table. By exploring the distinct attributes of each spreading method, a much deeper understanding into the world of light weight aluminum casting can be obtained, shedding light on the optimum method for accomplishing precision results in various applications.
Die Casting Refine
The Pass Away Casting Process is a highly effective manufacturing technique for generating geometrically complicated steel parts with high accuracy and repeatability. This process entails forcing liquified steel into a steel mold tooth cavity under high pressure. The mold, also referred to as a die, is typically made in two parts: the cover die fifty percent and the ejector die fifty percent. These passes away are developed to develop the wanted shape of the end product.
Among the key benefits of die casting is its capacity to create get rid of thin wall surfaces, complex information, and smooth surfaces. This makes it a favored option for markets such as automobile, aerospace, and electronic devices where complicated metal components are needed. In addition, pass away casting offers exceptional dimensional precision, allowing for marginal post-processing requirements.
Furthermore, pass away casting can be categorized right into warm chamber and cold chamber pass away casting procedures. In hot chamber die casting, the liquified metal is consisted of in a heater while in cold chamber die casting, the liquified steel is ladled right into the chilly chamber for each and every shot. aluminum casting. Each approach has its own set of benefits and is picked based on the particular needs of the task
Sand Spreading Technique
Utilizing a centuries-old technique, the sand spreading technique is a widely used procedure in the production industry for producing steel elements. This technique entails producing a mold made of compacted sand right into which molten metal is poured, permitting it to take the shape and strengthen of the mold dental caries. Sand spreading is valued for its versatility, as it can produce a variety of complex sizes and shapes, making it suitable for different industries such as auto, aerospace, and art foundries.
Regardless of its lengthy history, modern-day innovations in sand spreading strategies, such as the use of computer simulations for mold design and 3D printing for creating complex patterns, have better boosted the accuracy and performance of the procedure. Overall, the sand casting method stays a popular option for suppliers looking for a economical and reliable means to generate premium metal components.
Financial Investment Casting Technique
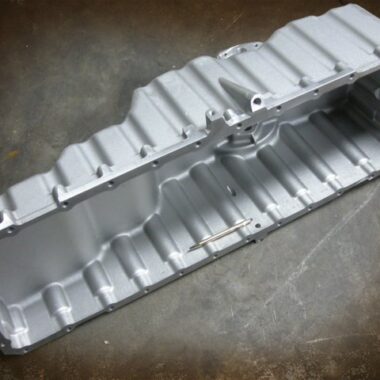
This strategy is preferred for its capacity to produce complex shapes with high accuracy and great surface area finishes. Industries such as aerospace, automobile, and precious jewelry count on investment casting for parts that require limited tolerances and complex information. The procedure permits cost-effective manufacturing of small to medium-sized components in numerous products, making it a flexible option for manufacturers seeking precision outcomes.
Irreversible Mold And Mildew Spreading
With a concentrate on producing steel elements with a recyclable mold, Long-term Mold and mildew Spreading supplies a different approach to the complex precision of financial investment spreading. aluminum casting. This approach, likewise called gravity pass away casting, involves using a permanent metallic mold and mildew commonly made from steel or actors iron. The mold is preheated before here the molten metal is poured right into it, enabling for faster solidification contrasted to sand spreading
Irreversible Mold Casting makes it possible for the production of high-quality, dimensionally accurate components with a great surface area finish. By making use of a reusable mold, producers can accomplish expense financial savings over time as the mold can be made use of numerous times without significant damage. This procedure is suitable for high-volume manufacturing runs where uniformity and effectiveness are critical.
Among the crucial advantages of Permanent Mold and mildew Spreading is its capacity to create complicated shapes and elaborate layouts with convenience. aluminum casting. The approach is extensively utilized in the automotive, aerospace, and electronics sectors for producing components such as engine components, warmth sinks, and structural elements

Centrifugal Spreading Method
The Centrifugal Casting Method is a method that includes revolving a mold at high rates while putting molten metal right into it. This process uses centrifugal force to disperse the molten metal equally along the walls of the mold, resulting in a high-quality, dense casting. The centrifugal pressure pushes contaminations and gases in the direction of the inner size of the casting, leading to a cleaner last item with boosted mechanical homes.
One of the vital benefits of centrifugal spreading is the capacity to generate disk-shaped or cylindrical parts with a fine-grained framework that enhances the mechanical properties of the casting. This technique is particularly ideal for developing symmetrical parts such as rings, pipelines, and tubes. Furthermore, centrifugal spreading provides the advantage of being a cost-efficient procedure with relatively low tooling expenses compared to various other casting approaches.
Conclusion
In verdict, recognizing the different sorts of light weight aluminum casting processes is crucial for attaining specific cause production. Each technique has its very own benefits and restrictions, making it essential to choose the most appropriate process based on the certain requirements of the task. Whether it is pass away spreading, sand spreading, financial investment casting, irreversible mold and mildew spreading, or centrifugal spreading, selecting the right technique can cause top notch and cost-effective manufacturing outcomes.
From die casting to sand spreading, financial investment spreading, long-term mold and mildew spreading, and centrifugal spreading, each technique brings its very own collection of advantages and details to the table. By exploring the unique features of each casting method, a much deeper insight right visit here into the globe of aluminum spreading can be gotten, dropping light on the optimum technique for attaining accuracy outcomes in numerous applications.
In hot chamber pass away spreading, the liquified steel is had in a furnace while in cool chamber die casting, the molten metal is ladled into the cool chamber for each shot.With a focus on producing steel parts via a here are the findings reusable mold, Irreversible Mold Casting uses an alternate technique to the intricate precision of investment spreading. Whether it is pass away spreading, sand casting, investment spreading, permanent mold spreading, or centrifugal casting, choosing the ideal technique can lead to economical and top notch manufacturing results.
Report this page